IoT and Industrial Automation: Driving Efficiency in Manufacturing
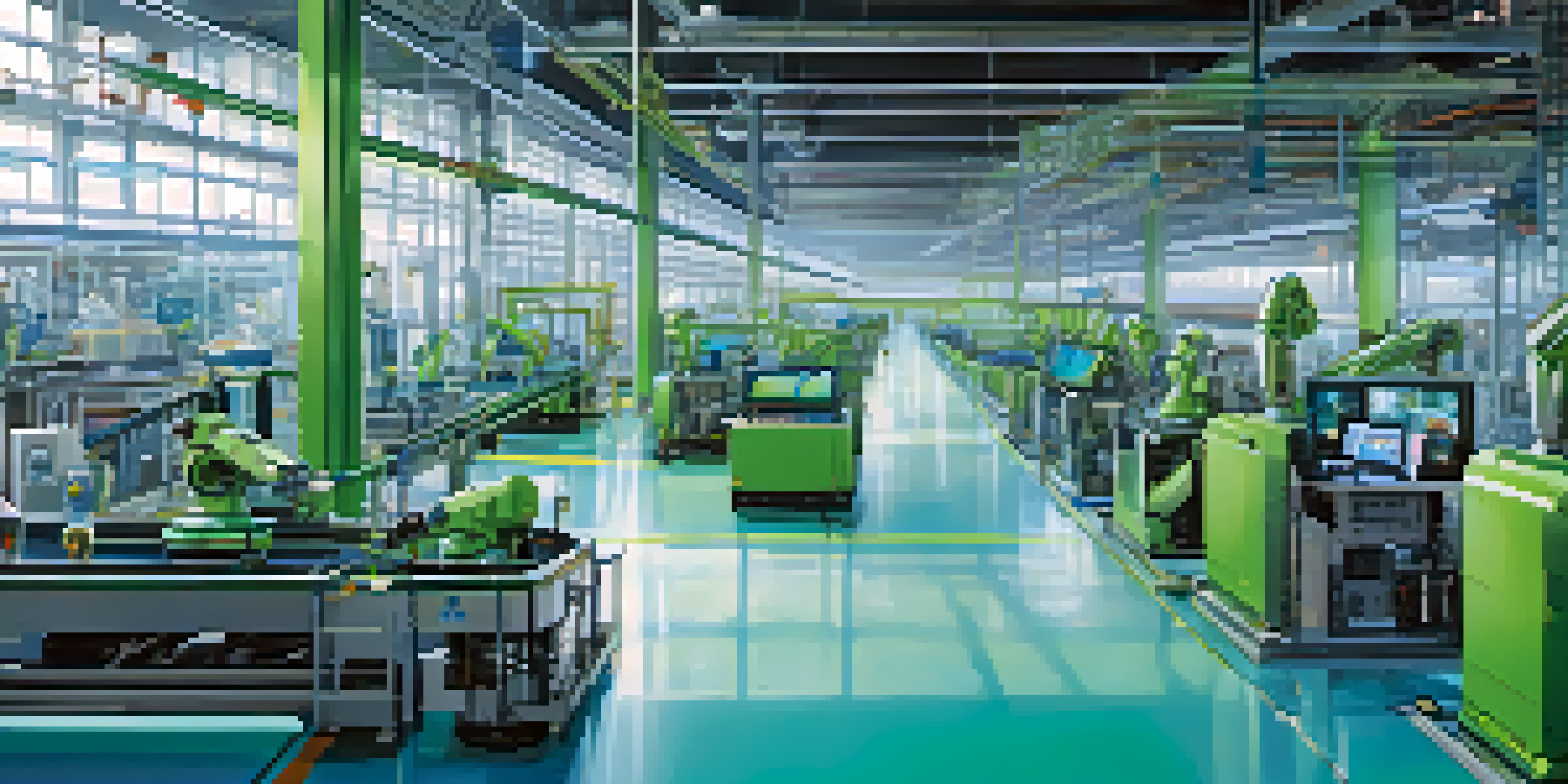
Understanding IoT in the Manufacturing Landscape
The Internet of Things (IoT) refers to a network of interconnected devices that communicate and exchange data. In manufacturing, this means machines, sensors, and software can work together seamlessly. Imagine a factory where every machine can 'talk' to one another, sharing vital information about performance and maintenance needs.
The Internet of Things is not a concept; it is a way of life that has the potential to transform industries and improve efficiency.
This connectivity allows manufacturers to monitor operations in real-time, leading to quicker decision-making. For instance, if a machine starts showing signs of wear, the IoT system can alert the operators before a breakdown occurs. This proactive approach not only reduces downtime but also saves on costly repairs.
Related Resource
As manufacturers embrace IoT, they gain a competitive edge. By leveraging data analytics and machine learning, companies can refine their processes, optimize production schedules, and enhance overall efficiency. The future of manufacturing is not just about machines; it's about smart machines.
The Role of Automation in Modern Manufacturing
Industrial automation involves using control systems like computers and robots to handle different processes and machinery. By integrating automation with IoT, manufacturers can create smarter production lines. Picture a car assembly line where robots adjust their tasks based on real-time data from sensors monitoring the assembly process.
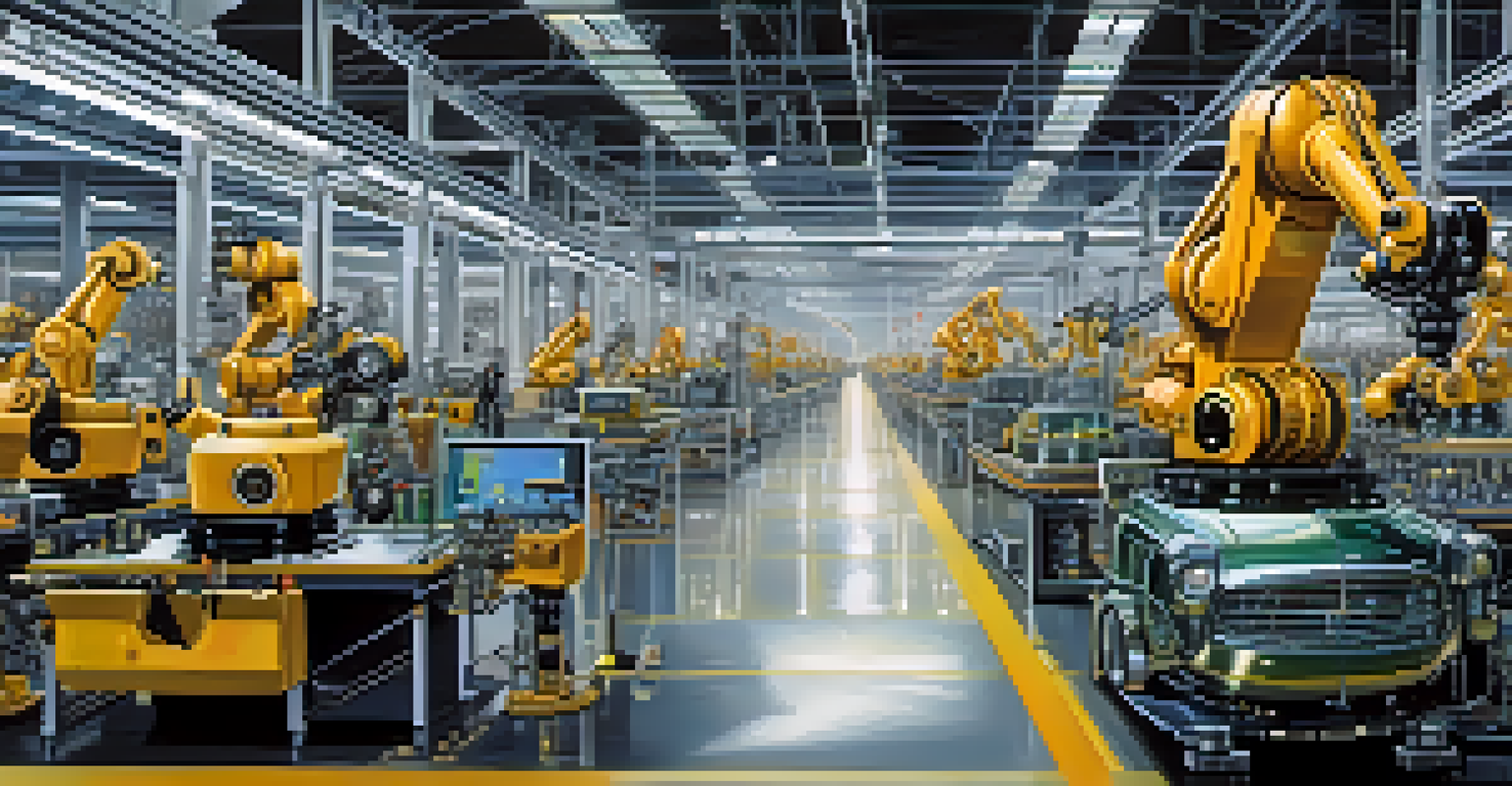
This level of automation not only speeds up production but also improves accuracy. With precise data at their fingertips, manufacturers can minimize human error and ensure a consistently high-quality product. For example, a slight adjustment in a robot's operation can lead to significant improvements in the final output.
IoT Boosts Real-Time Monitoring
The Internet of Things enables manufacturers to monitor machine performance in real-time, allowing for proactive maintenance and reduced downtime.
Moreover, automation frees up human workers from repetitive tasks, allowing them to focus on more strategic roles. This shift can lead to job enrichment, where employees engage in more fulfilling work, ultimately enhancing job satisfaction and productivity.
Enhancing Efficiency Through Predictive Maintenance
One of the standout benefits of IoT in industrial automation is predictive maintenance. Instead of following a fixed schedule for machine maintenance, IoT devices can analyze usage patterns and predict when a machine is likely to fail. Imagine being able to replace a part just before it breaks down, avoiding unexpected downtime.
Automation is no longer a choice; it is a necessity for survival and success in today’s manufacturing landscape.
This approach not only saves money on repairs but also extends the lifespan of machinery. By ensuring equipment is maintained based on actual performance data, manufacturers can avoid the costs associated with emergency repairs and lost production time. It's like getting a warning light on your car before a major issue arises.
Related Resource
As a result, predictive maintenance helps streamline operations, leading to a more efficient manufacturing process. Companies can allocate resources more effectively, ensuring that maintenance teams are deployed only when necessary, further enhancing productivity.
Data-Driven Decision Making in Manufacturing
Data is the new gold in the manufacturing world, especially when combined with IoT and automation. Access to real-time data allows manufacturers to make informed decisions quickly. Think of it like having a live dashboard that provides insights into every aspect of the production process.
With this wealth of information, manufacturers can identify bottlenecks, track performance metrics, and fine-tune operations on-the-fly. For instance, if a specific machine is running slower than usual, adjustments can be made instantly to rectify the issue. This agility is crucial in today’s fast-paced market.
Automation Enhances Production Efficiency
Integrating automation with IoT creates smarter production lines, improving speed and accuracy while freeing up human workers for more strategic tasks.
Ultimately, data-driven decision-making fosters a culture of continuous improvement. Manufacturers who harness this power can stay ahead of their competitors, adapting to changes in demand and ensuring they meet customer expectations efficiently.
Connecting the Supply Chain with IoT
IoT doesn't just improve manufacturing processes; it also strengthens supply chain management. By connecting suppliers, manufacturers, and distributors through IoT devices, companies can enhance visibility across the entire supply chain. Imagine tracking a product's journey from raw materials to the finished goods in real-time.
This level of transparency allows manufacturers to respond quickly to supply chain disruptions, such as delays in shipping or inventory shortages. For example, if a supplier is running low on materials, an IoT system can alert the manufacturer, enabling them to adjust production schedules accordingly.
Related Resource
Additionally, enhanced supply chain connectivity can lead to better collaboration among partners. With everyone on the same page, companies can streamline operations, reduce lead times, and ultimately improve customer satisfaction.
The Impact of IoT on Workforce Dynamics
The integration of IoT and automation significantly affects workforce dynamics in manufacturing. As machines take over repetitive tasks, employees can shift their focus to more complex and creative roles. This transition can lead to a more engaged workforce, as employees feel their skills are being utilized effectively.
However, this shift also requires reskilling and upskilling workers to adapt to new technologies. Manufacturers must invest in training programs to ensure their workforce is equipped to handle advanced machinery and data analytics tools. It's akin to upgrading your phone; the new features require a bit of learning to fully enjoy.
Data Drives Informed Decisions
Access to real-time data empowers manufacturers to make quick, informed decisions, fostering a culture of continuous improvement and adaptability.
By fostering a culture of continuous learning, manufacturers can build a resilient workforce ready to tackle the challenges of modern production. This investment in people not only enhances productivity but also boosts employee morale and retention.
Challenges and Considerations for IoT Implementation
While the benefits of IoT in industrial automation are substantial, there are challenges to consider during implementation. One major hurdle is the integration of new technologies with existing systems. Manufacturers must ensure that their current infrastructure can support IoT devices, which can sometimes require significant investment.
Additionally, cybersecurity is a pressing concern. As more devices connect to the internet, the risk of cyber threats increases. Manufacturers must prioritize safeguarding their systems against potential breaches, just as you would lock your doors to protect your home.
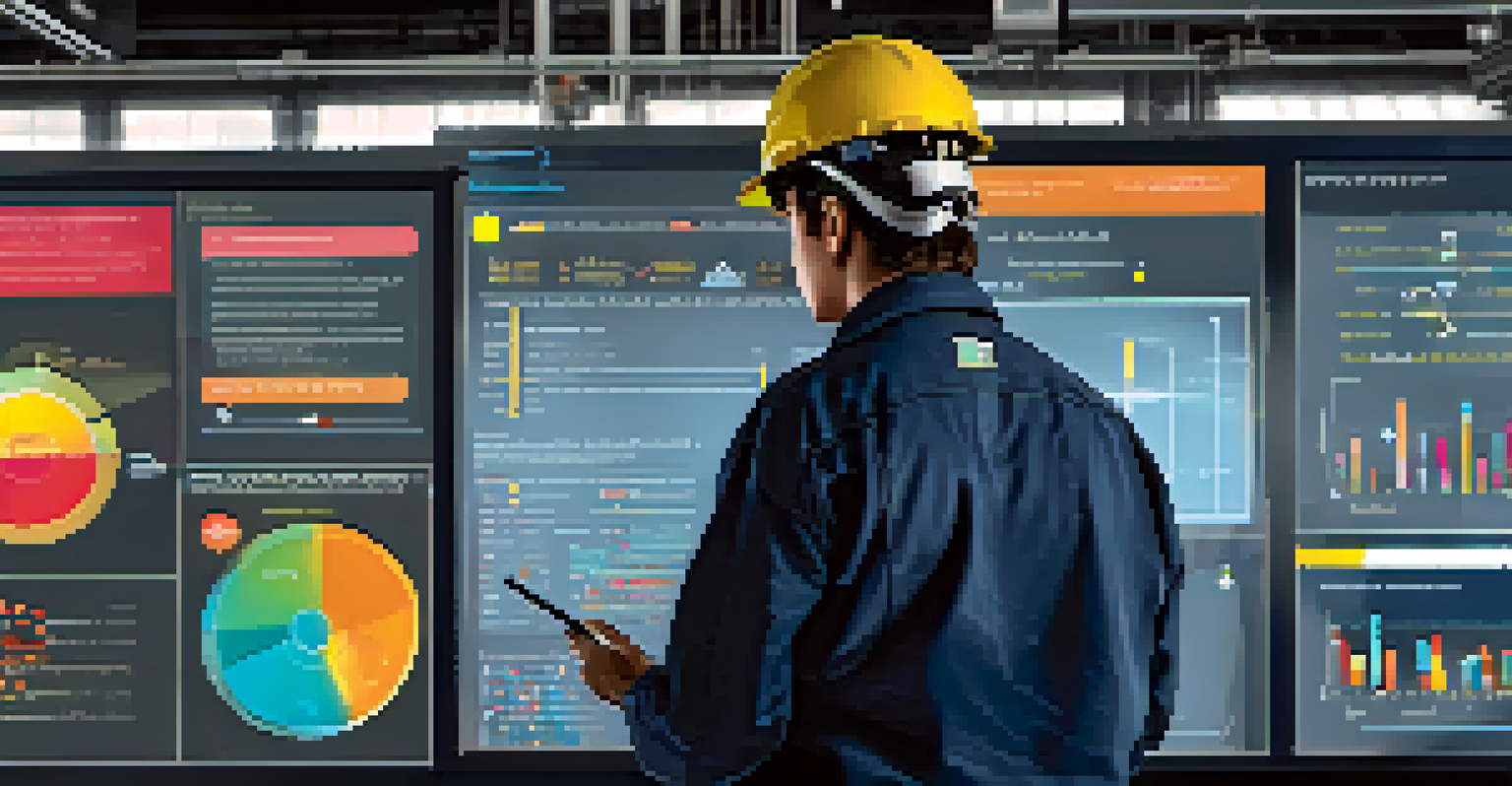
Lastly, change management is crucial for successful IoT implementation. Employees may resist new technologies out of fear of job loss or difficulty adapting. To combat this, companies should foster open communication and provide support throughout the transition, ensuring everyone understands the benefits of IoT in enhancing their work.